The Comprehensive Guide to Die Cast Mold Manufacturers
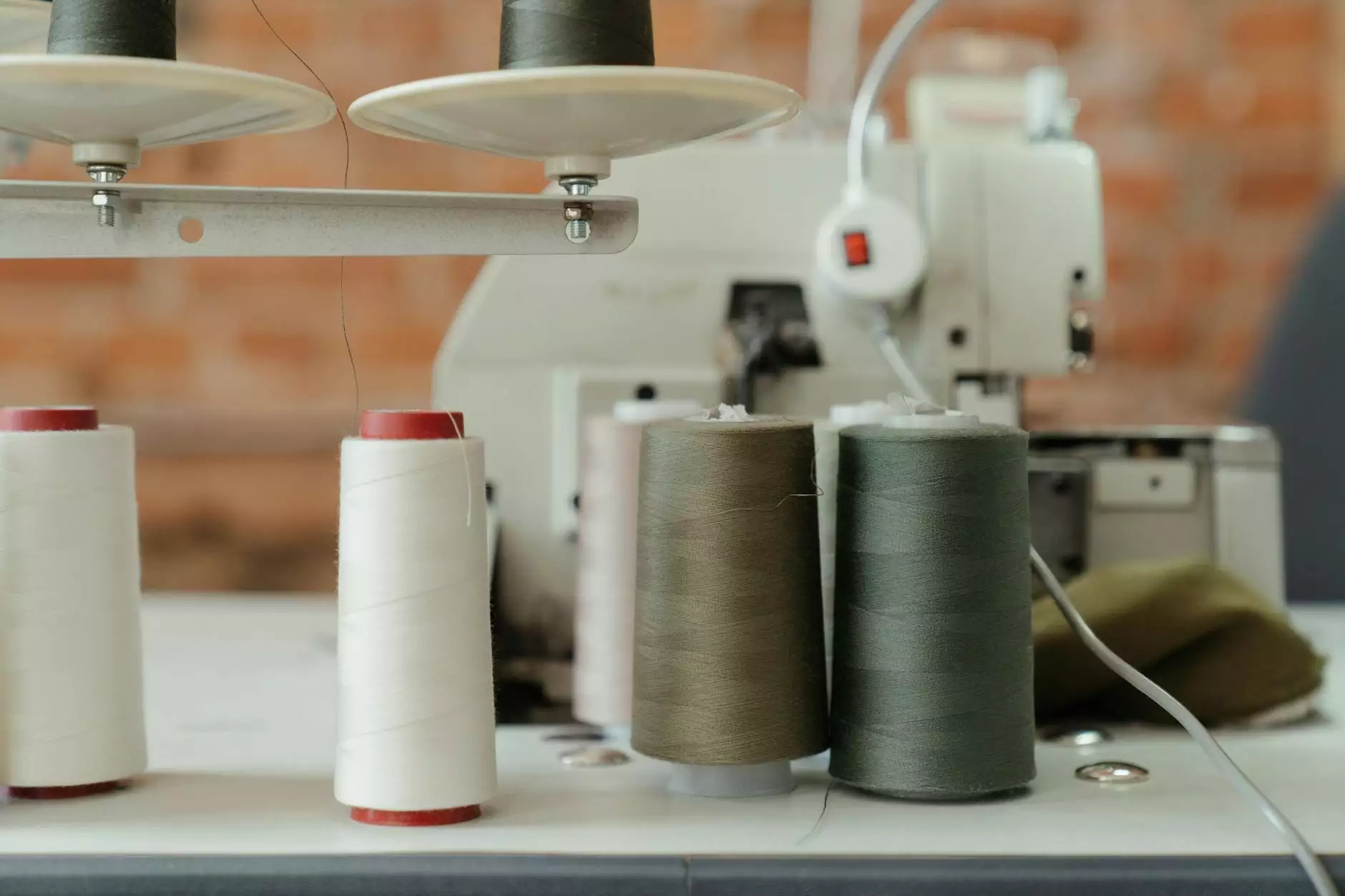
In the dynamic and ever-evolving landscape of manufacturing, die cast mold manufacturers play a pivotal role in the production of high-quality metal components. These specialized manufacturers are essential for industries ranging from automotive to electronics, enabling the mass production of intricate shapes and designs with remarkable precision and efficiency. In this extensive article, we will delve deep into the methodologies, advantages, and future trends associated with die casting, equipping your business with the knowledge necessary to stay competitive and informed.
Understanding Die Casting
Die casting is a metal casting process that employs molten metal, forcing it into a steel mold, or "die," under high pressure. This technique is renowned for its ability to produce parts with superior dimensional accuracy and smooth surface finishes, making it ideal for various applications.
How Die Casting Works
The die casting process can be outlined in several key steps:
- Preparation of the Die: The die, typically made of hardened steel, is meticulously manufactured and polished to ensure that the desired shape, texture, and tolerances are met.
- Melting the Metal: Metal alloys, commonly aluminum, zinc, and magnesium, are heated to their melting points in a furnace.
- Injection of Molten Metal: The molten metal is injected into the die under intense pressure, filling the mold cavity quickly.
- Cooling and Solidification: The metal cools and solidifies, taking the shape of the die. Cooling times can vary based on the size and complexity of the part.
- Opening the Die: Once cooled, the die is opened, and the cast part is ejected.
- Finishing Processes: Further processes, such as machining, surface finishing, and coating, may be conducted to achieve the final desired product quality.
Advantages of Die Casting
There are several reasons why die casting is preferred by manufacturers across various sectors:
- High Precision and Accuracy: The pressure involved in die casting allows for tight tolerances and superior repeatability, making it an ideal choice for precision components.
- Complex Geometries: Die casting can accommodate complex shapes that would be difficult or impossible to create using other manufacturing methods.
- Reduced Production Time: Die casting is suited for high-volume production runs due to its efficiency and speed, significantly reducing lead times.
- Material Versatility: While aluminum and zinc are predominant, a wide variety of alloys can be used, allowing for tailored properties and characteristics.
- Enhanced Surface Finish: The die casting process results in parts with high-quality surface finishes, often requiring less post-processing.
Key Applications of Die Casting
Die casting is utilized across diverse industries, including:
- Automotive Industry: Components such as engine blocks, gearboxes, and housings are frequently produced using die casting.
- Aerospace: Aircraft parts must meet stringent quality and weight specifications, making die casting an essential manufacturing method.
- Electronics: Die cast housings for electronic devices provide protection while allowing for intricate designs.
- Consumer Goods: Many everyday products are manufactured using die casting, including tools, hardware, and appliances.
Choosing the Right Die Cast Mold Manufacturer
When selecting a die cast mold manufacturer, businesses should consider several critical factors to ensure they partner with a capable and reliable source:
- Experience and Technical Expertise: Look for manufacturers with a proven track record and extensive experience in die casting.
- Quality Certifications: Ensure that the manufacturer adheres to industry standards, such as ISO certification.
- Portfolio of Work: Review their previous projects to assess their capability in producing similar components.
- Production Capacity: Evaluate the manufacturer's ability to meet your volume requirements, especially for large production runs.
- Customer Support: Strong communication and support systems are vital for effective collaboration throughout the production process.
Innovation and Future Trends in Die Casting
As technology continues to advance, the die casting industry is witnessing significant innovations that enhance efficiency and sustainability:
Automation and Industry 4.0
Automation in die casting is on the rise, with the integration of Industry 4.0 technologies, including:
- Robotics: Automated systems are increasingly used for handling, loading, and unloading, reducing labor costs and increasing safety.
- IoT Integration: Internet of Things (IoT) devices are employed to monitor equipment and processes in real-time, enhancing predictive maintenance and reducing downtime.
- Data Analytics: Advanced data analytics help manufacturers optimize processes and identify areas for improvement, leading to better quality control.
Sustainability and Materials
As sustainability becomes a priority, die cast mold manufacturers are adopting eco-friendly practices, such as:
- Recycling Materials: Many manufacturers are using recycled metals, reducing waste and environmental impact.
- Energy-efficient Processes: Innovations aimed at decreasing energy consumption during production are being implemented.
Conclusion: The Role of Die Cast Mold Manufacturers in Modern Industry
In conclusion, die cast mold manufacturers are integral to the modern manufacturing landscape, enabling the production of complex and precise metal components across a variety of industries. By understanding the die casting process, benefits, applications, and innovations, businesses can make informed decisions to harness the potential of die casting for their production needs.
Investing in partnerships with the right die cast mold manufacturers can pave the way for enhanced product quality, efficiency, and competitive advantage in the marketplace. As industries continue to evolve, staying abreast of trends in die casting will ensure that your business remains poised for success.
For comprehensive solutions in die casting and metal fabrication, consider exploring the offerings by deepmould.net.