Understanding LOLER Compliance in South Wales
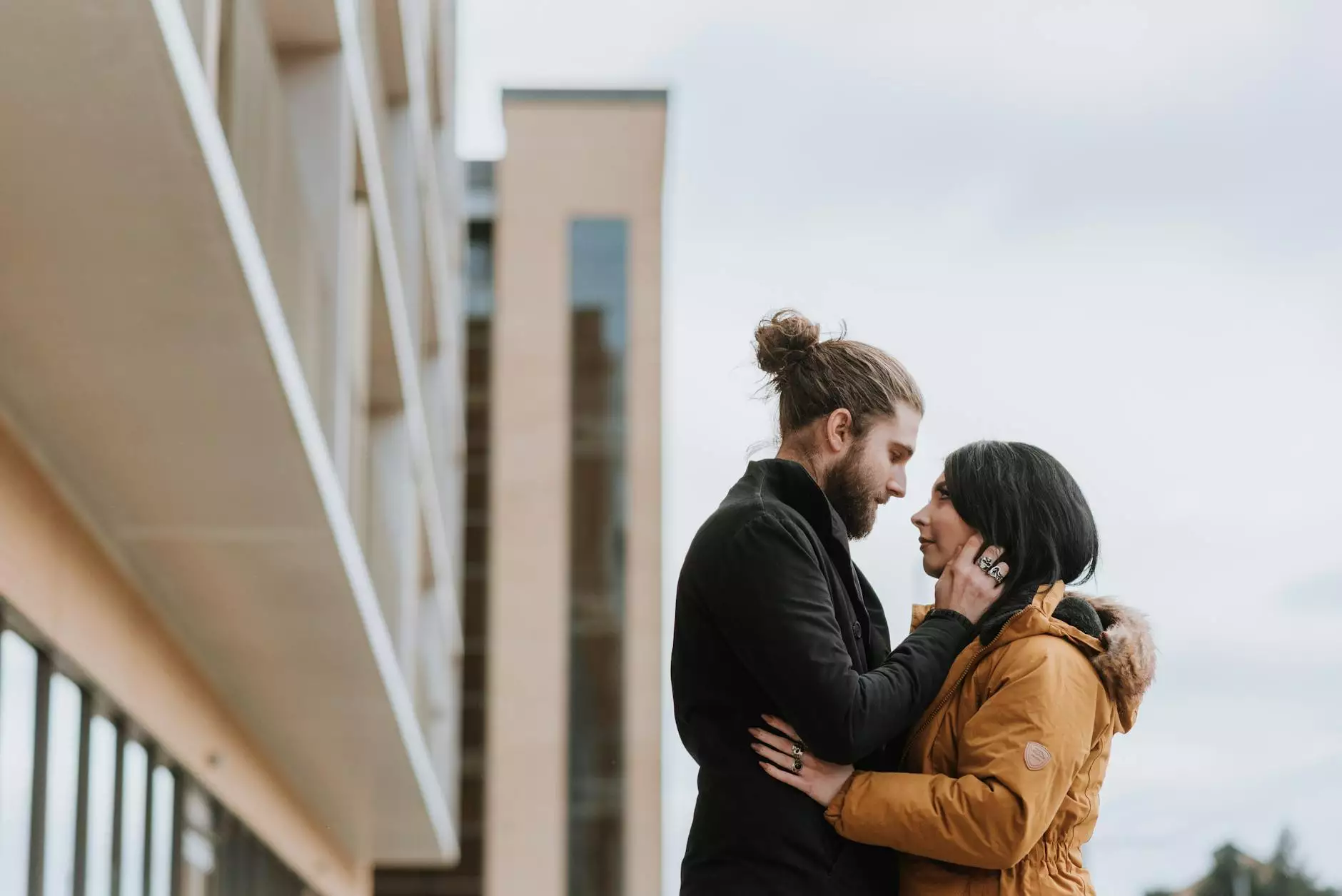
The concept of LOLER compliance is pivotal for ensuring safety and regulatory adherence for businesses across various sectors, particularly in South Wales. This article delves deeply into what LOLER compliance entails, its significance for businesses in the Home & Garden, Gardeners, and Pest Control categories, and how companies can effectively manage their compliance obligations.
What is LOLER Compliance?
The acronym LOLER stands for the Lifting Operations and Lifting Equipment Regulations, which was enacted in 1998 in the UK. The LOLER regulations are designed to ensure that all lifting equipment used in the workplace is safe and fit for purpose. This includes everything from cranes and hoists to forklifts and lifting slings.
The Significance of LOLER Compliance
For businesses, particularly those operating within the Home & Garden, Gardeners, and Pest Control sectors, adhering to LOLER regulations is not just a legal obligation; it is also essential for several reasons:
- Safety: Compliance ensures that lifting equipment is properly maintained and regularly inspected, preventing accidents and injuries in the workplace.
- Legal Protection: Adhering to LOLER not only protects employees but also safeguards businesses against legal repercussions arising from workplace accidents.
- Enhanced Reputation: Businesses that prioritize safety can enhance their reputation, fostering trust and reliability among clients and customers.
- Operational Efficiency: Regular inspections and maintenance foster efficient operations, reducing downtime and increasing productivity.
LOLER Compliance and Its Application in Different Sectors
1. Home & Garden Businesses
In the Home & Garden industry, companies often utilize lifting equipment such as garden cranes, lifts for heavy appliances, and more.
Adhering to LOLER compliance is crucial for:
- Equipment Safety: Ensure that garden machinery and lifting devices are capable of safely lifting and moving heavy objects.
- Customer Safety: Protecting customers and clients from accidents when lifting is an integral part of service delivery.
- Insurance Requirements: Many insurance policies require proof of compliance to handle claims related to workplace injuries involving lifting equipment.
2. Gardeners
Gardeners, particularly those who manage large landscapes or commercial properties, often rely heavily on various lifting devices.
Key aspects of LOLER compliance in this role include:
- Regular Inspections: Lifting gear such as pulley systems or hoisting equipment needs regular inspections to ensure they are safe for ongoing use.
- Training and Certification: Gardeners must be trained to use lifting equipment safely and maintain compliance with LOLER regulations.
- Risk Assessments: Conducting regular risk assessments ensures that equipment used is effective and compliant.
3. Pest Control Businesses
Pest control businesses may utilize lifting equipment for accessing elevated spaces, such as roofs or high tree branches. This requires strict adherence to LOLER regulations.
Points to consider include:
- Access Equipment: Use of cherry pickers or scaffolding must comply with LOLER guidelines to ensure safety during operations.
- Documentation: Keeping detailed records of inspections and maintenance is essential for regulation compliance and business audits.
The Compliance Process: Steps for Businesses in South Wales
Step 1: Assess Your Equipment
The first step towards achieving LOLER compliance is to conduct a thorough assessment of all lifting equipment used in your operations. Determine the types of equipment, their usage, and the potential risks involved.
Step 2: Implement Regular Inspections and Maintenance
It is vital to institute a routine inspection schedule to ensure that all lifting equipment is regularly checked by a qualified person. Documentation of these inspections should be meticulously maintained for legal compliance.
Step 3: Train Your Staff
Staff training is crucial for compliance. Ensure staff are aware of safe lifting practices, the dangers associated with improper lifting, and the importance of reporting defective equipment immediately.
Step 4: Documentation and Record Keeping
Maintain detailed records of all inspections, maintenance, and usage of lifting equipment. This not only assists in compliance but also protects the business in case of legal scrutiny.
Step 5: Seek Professional Guidance
If your business lacks the expertise to handle LOLER compliance effectively, consider seeking professional consultation. Compliance specialists can provide invaluable assistance in ensuring all regulations are followed.
FAQs About LOLER Compliance in South Wales
What Types of Equipment Does LOLER Apply To?
LOLER applies to any equipment used for lifting or lowering loads. This includes, but is not limited to, cranes, hoists, elevators, lifts, and even slings and other accessories.
How Often Should Equipment Be Inspected?
Equipment should be inspected at regular intervals, which can vary based on the type of equipment and its usage. Generally, a thorough examination is required at least once every six months.
What are the Consequences of Non-compliance?
Non-compliance with LOLER regulations can result in severe penalties, including fines and prosecution, as well as damaging the reputation of the business.
Conclusion
Compliance with LOLER regulations is an essential aspect of operating safely and legally in South Wales, especially for businesses in the Home & Garden, Gardeners, and Pest Control sectors. By ensuring proper training, regular inspections, and rigorous adherence to safety standards, businesses can not only protect their employees and clients but also enhance their operational efficiency and market reputation.
For companies looking for expert advice and assistance in achieving LOLER compliance, trusted local businesses such as Safe Plant UK provide invaluable services to streamline compliance and ensure safety standards are upheld.
loler compliance south wales