Revolutionizing the Automotive Industry with Injection Molding
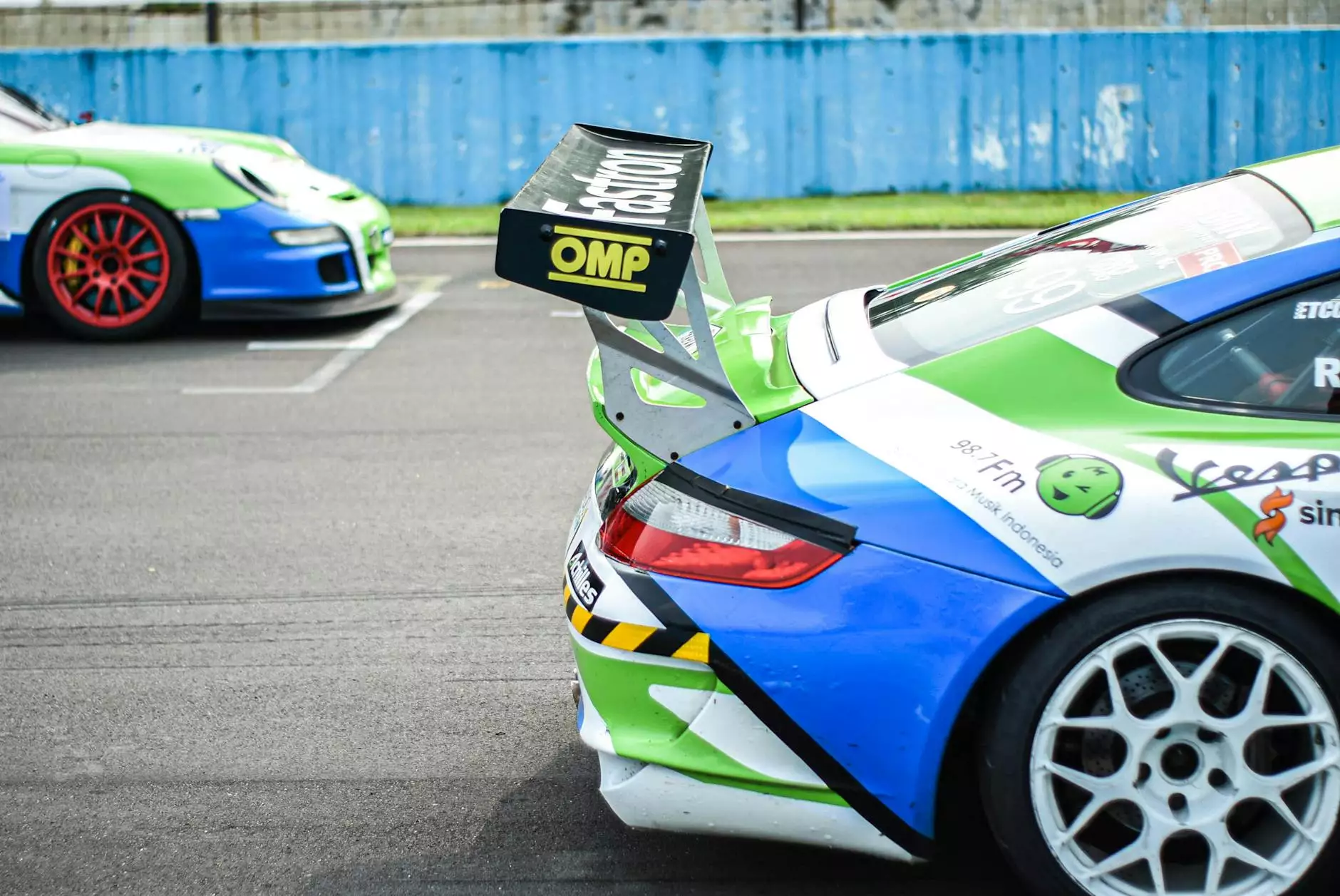
The future of the automotive industry is bright and streamlined, thanks to the innovative processes that are continuously being developed. Automotive injection molding has emerged as a game-changer in this realm, revolutionizing the way automotive parts are produced. This article will delve deep into the ins and outs of injection molding, its benefits, and why it is essential for modern automotive manufacturing, particularly for metal fabricators.
The Basics of Automotive Injection Molding
Injection molding is a manufacturing process that has been optimized for various industries, but it holds particular significance in the automotive sector. The process involves:
- Heating plastic materials until they become molten.
- Injecting the molten plastic into a mold to form a specific shape.
- Allowing it to cool and solidify before ejecting the final product.
This method allows for the mass production of high-quality automotive parts that require precision, repeatability, and consistency. From dashboards to body panels, the versatility of injection molding provides significant advantages over traditional manufacturing techniques.
Key Advantages of Automotive Injection Molding
There are numerous benefits associated with the use of automotive injection molding in the production of parts. Here are some of the most impactful:
1. Enhanced Efficiency
One of the most notable advantages of injection molding is its ability to produce large quantities of parts in a relatively short time frame. Compared to other manufacturing processes, the speed and efficiency of injection molding can result in significant cost savings and reduced production times.
2. Superior Quality and Precision
Injection molding allows for highly precise and intricate designs. The molds are crafted to exact specifications, ensuring that every part produced maintains a high level of uniformity and quality control. This is especially important in the automotive industry, where safety and performance are paramount.
3. Cost-Effectiveness in Large Production Runs
While there may be a higher initial setup cost for the mold itself, the cost-per-part decreases significantly with larger production runs. This makes automotive injection molding especially appealing for manufacturers needing to produce large quantities of parts.
4. Material Versatility
Injection molding can work with a wide variety of materials, including various plastics and composites. This flexibility allows manufacturers to select materials that best suit their specific requirements and performance criteria.
5. Environmentally Friendly Options
Many modern injection molding processes utilize recycled materials, reducing waste and minimizing the environmental impact associated with production. This aligns with the automotive industry's growing emphasis on sustainability and eco-friendliness.
Application of Automotive Injection Molding in the Industry
The applications for automotive injection molding are vast and varied. Here are some common areas where injection-molded parts are used:
- Exterior Components: This includes body panels, bumpers, and trim elements.
- Interior Parts: Dashboards, consoles, and decorative elements benefit from precise molding.
- Functional Components: Items such as housings for headlights, taillights, and electronic components.
- Under-the-hood Components: Parts like air intake manifolds and ducting systems.
- Automotive Accessories: Custom parts designed for added features or enhancements.
Challenges and Considerations in Injection Molding
Despite its many advantages, automotive injection molding does have challenges that manufacturers should consider:
1. Initial Setup Costs
The creation of injection molds can require a significant investment. However, this cost can often be offset by the long-term savings achieved through mass production.
2. Design Limitations
Certain design characteristics may be challenging to achieve with injection molding. For example, parts with complex geometries may require additional engineering and modification to be suitable for mass production.
3. Production Constraints
While injection molding is efficient, there are limitations regarding how quickly molds can be adjusted or replaced. If production needs change rapidly, this can pose difficulties for manufacturers.
Why Choose Deepmould for Your Injection Molding Needs?
Deepmould.net is a leading provider of metal fabrication and injection molding solutions. With a commitment to quality, precision, and customer satisfaction, Deepmould has become a trusted partner for automotive manufacturers. Here’s why Deepmould stands out:
- Expertise: Our team is made up of industry experts who understand the nuances of injection molding and its applications in automotive manufacturing.
- State-of-the-art Technology: We leverage the latest technologies and equipment to ensure that every part we produce meets the highest standards of quality.
- Customization: We understand that every project is unique, and we offer tailored solutions to meet the specific needs of our clients.
- Sustainability: At Deepmould, we prioritize environmentally friendly practices in all our operations, ensuring that our processes align with sustainability goals.
- Competitive Pricing: Our pricing strategies are designed to provide the best value without compromising quality.
The Future of Automotive Injection Molding
The landscape of the automotive industry is constantly evolving, and automotive injection molding is undoubtedly part of this dynamic shift. As manufacturers continue to seek ways to improve efficiency, reduce costs, and enhance sustainability, injection molding will maintain its pivotal role. Innovations in materials, such as bio-based plastics and advanced composites, will widen the applications of injection molding even further.
1. Technological Advancements
With ongoing advancements in robotics and automation, the injection molding process will become even more refined. This could result in faster cycle times and even greater efficiency, further reducing costs for automotive manufacturers.
2. Shift Toward Sustainability
The automotive industry is increasingly focused on incorporating green practices into manufacturing. Injection molding can play a vital role in this transition by utilizing recycled materials and reducing waste through efficient production methods.
3. Customization and Personalization
As consumers demand more personalized vehicles, the flexibility offered by injection molding will allow manufacturers to create custom parts and accessories that enhance the consumer experience.
Conclusion
Automotive injection molding is not just a manufacturing method; it is a transformative technology that is shaping the future of the automotive industry. With its capacity for high-volume production, cost efficiencies, and precision manufacturing, it empowers automotive companies to thrive in a competitive landscape. As the industry continues on its path of innovation, providers like Deepmould.net are well-equipped to lead the way in offering top-tier injection molding services tailored to the evolving needs of the automotive market.
By embracing the potential of automotive injection molding, manufacturers are not only enhancing efficiency and quality but also paving the way for a more sustainable and innovative automotive future.